生産技術力
Sheet Metal
-
- 01
-
お問い合わせ・打合せ・お見積り・受注
お問い合わせいただいた内容をもとに、製作提案等の打合せを行い、お見積りをお出しします。 お見積りの条件に問題がなければ、注文書をいただき受注となります。
-
- 02
-
受注登録
お客様からいただいた注文書をもとに、生産進捗管理システムに受注登録します。 製品ごとに作業指示書を発行し、バーコードにて作業進捗管理を行っております。
-
- 04
-
表面処理
塗装・メッキ等の表面処理もお任せください。協力工場との連携で幅広い表面処理が可能です。 窒化処理等の熱処理にも対応いたします。ぜひご相談ください。
-
- 05
-
検査
工程の各段階で品質チェックを実施していますが、出荷前に改めて最終検査を行います。 お客様の要求に応じた、検査方法で品質を管理しています。
-
- 06
-
洗浄・出荷
最終検査を完了した製品は出荷前に洗浄を行います。 洗浄後にフィルムやエアキャップなどで丁寧に包装し、お客様のもとに出荷いたします。
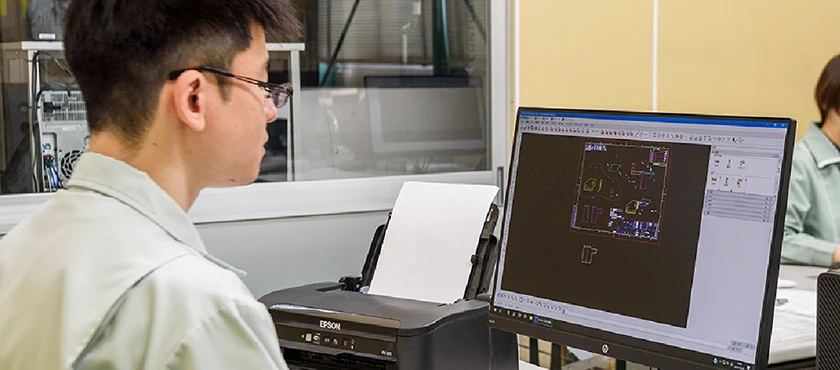
プログラムProgram
精密板金加工における板金展開技術は、製品の形状を作り出すための重要な工程です。
曲げ工程や溶接工程で必要とされる情報などを考慮し、最適な展開データを作成します。
-
2D・3D CADデータの活用
受注図面から、レーザー加工機で切断するための展開データを作成しますが、CADデータを支給していただくと、正確な展開データをスムーズに作成することができます。
-
当社では、各種CADデータに対応しております
2Dデータ(dxf・dwg 等)
3Dデータ(sldprt・ iges・step・X_T 等) -
溶接長の最小化による精度、コスト改善
立体的な形状を作るために、溶接を行いますが、製品の形状によっては溶接距離が長くなる場合があり、その結果、溶接熱によって板金部品が大きく歪み変形する可能性があります。
溶接による歪みを最小限に抑えるために、製品の分割方法を検討し、溶接長を少なくする展開を行っています。 -
NCデータネットワーク
作成したNCデータは、社内ネットワークによりレーザー加工機に転送されます。
-
治具レス加工
展開データ作成時、多品種少量生産での治具レス加工のために、部品の位置決めのためのマーキングやコイニング(ダボ)、抜き溝を利用したはめあい構造を採用しています。
加工時間の短縮と、治具にかかるコストを抑えることができます。-
レーザーマーキング位置決め
-
ダボ位置決め
-
はめあい構造
-
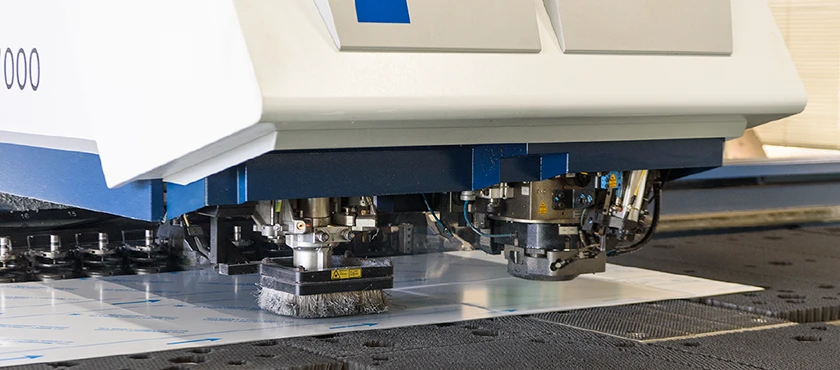
レーザーLaser
2台のパンチレーザー複合機と1台のレーザー専用機 計3台を保有し、
製品の「材質・板厚・数量」等を考慮しながら、最適な加工機を選択しています。
鉄、ステンレスはもとよりアルミ(ジュラルミン)、銅、真鍮、チタンなどの加工にも対応しています。
-
CO2レーザー(TruMatic 7000)
CO2レーザー加工機は、切断品質が非常に高く、とても滑らかな切断面を得ることができます。
薄板は保護フィルムなしで加工した場合、ステンレスでもアルミでも、ほとんどバリは発生しません。-
滑らかな切断面
-
-
ファイバーレーザー(TruMatic 3000fiber・TruLaser 3030fiber)
ファイバーレーザー加工機では、今まで切断不可とされていた純アルミ、ジュラルミン、銅、真鍮、チタンなどのレーザー加工が可能になりました。
また、CO2レーザーに比べ、高速かつ熱ひずみの少ない高品位な加工が可能です。-
左から A1050 A2017 C1100 C2801 TP340
-
-
レーザー加工実績
当社レーザー加工機の加工実績です。多種多様な材料の加工を行っております。
鉄 SPCC 0.5~3.2mm 鉄 SPHC 1.6~9.0mm 鉄 SS400 4.5~19.0mm 鉄 SECC 0.5~3.2mm ステンレス SUS304 0.1~12.0mm ステンレス SUS430 0.3~6.0mm アルミ A1050 0.3~3.0mm アルミ A2017 1.0~5.0mm アルミ A5052 0.3~10.0mm 銅 C1020、C1100 0.2~8.0mm 真鍮 C2710 0.2~6.0mm チタン TP340 0.3~3.0mm -
パンチレーザー複合機
パンチレーザー複合機は、パンチ加工とレーザー加工のそれぞれの機能を持つ加工機です。
パンチ加工では、金型を用いて穴あけやタップ加工などの打ち抜き加工を行い、レーザー加工では、外周の切断や複雑な形状の切断を行っています。
パンチ加工とレーザー加工を組み合わせることで、効率的で高品質な製品を加工することができます。 -
タップ・バーリング・絞り加工
パンチレーザー複合機で、タップ・バーリング・絞り加工行うことにより、高い精度を確保し生産性を向上することができます。
-
バーリング加工+タップ加工+レーザー加工
-
ダボ加工+レーザー加工
-
-
保護フィルム
当社では、ステンレス材やアルミニウム材は保護フィルム付きの材料を常時在庫しております。
保護フィルム付きの材料を使用することで、レーザー加工中や後工程で生じる可能性のあるキズやダメージを防止することができます。 -
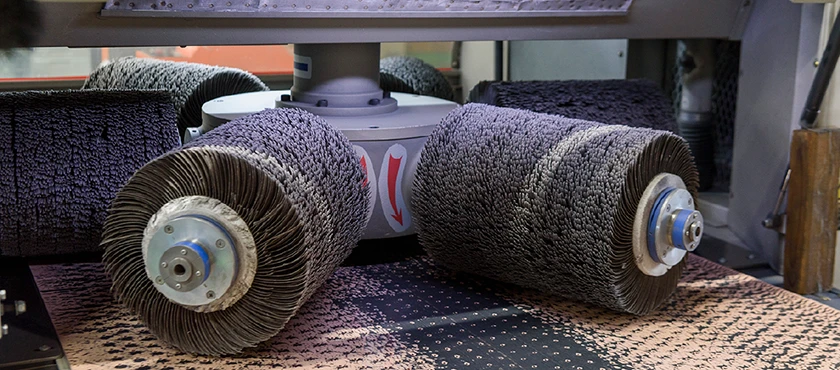
バリ取り・面取りDeburring・Chamfer
切断加工面の角部のバリ取りと面取りは、製品の品質に重要な役割を果たしています。
当社では、R面取り機能を搭載したバリ取り機を導入し、
バリ取りとともにエッジ部分の面取りも行っています。
-
均一なR面取り加工が可能
手作業とは異なり、バリ取り機を使用することでほぼ均一な面取りが可能になり、品質の安定化と外観性の向上につながっています。
-
R面取り前
-
R面取り後
-
-
生産性向上
複雑な形状の製品に対しては、手作業でのバリ取りには多くの時間が必要になりますが、バリ取り機を使用することにより、大幅な時間の短縮が計られ、生産性向上につながっています。
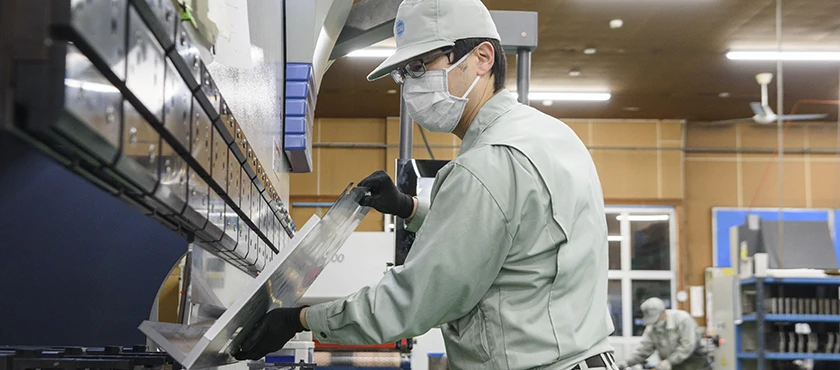
曲げBend
プレスブレーキは18トンから135トンの大型まで保有し、
最大3000ミリまで(板厚による)加工可能となっています。
幅広いニーズや複雑な曲げ加工にも対応できるよに、各種金型を保有しています。
-
各種曲げ
直角曲げ・鋭角まげ・鈍角まげ・R曲げ・ヘミング・段曲げ等、各種曲げに対応しています。
様々な曲げ技術を駆使して、製品を製作します。
(板厚・材質によって曲げに制限がある場合があります。お問い合わせください)-
直角曲げ
-
鋭角まげ
-
鈍角まげ
-
R曲げ
-
ヘミング
-
段曲げ
-
-
曲げキズ
ステンレス鏡面仕上げ材やヘアライン仕上げ材などを使用した外観製品は、曲げキズ防止シートを使用し、「曲げキズをつけない加工」を行い、製品全体の品質を向上させることができます。
-
-
曲げ加工の精度
曲げ加工後の溶接では、曲げの加工精度が溶接後の出来上がり精度に大きな影響を与えます。
それぞれの工程での寸法精度が累積されることで、製品の品質に問題が生じる可能性もあります。
当社の曲げスタッフは、高い技術力と豊富な経験で、高精度な加工を実現しています。 -
リピート品
保存した曲げデータを呼び出すことで、同じ加工を再現することが可能です。
これにより、品質を確保し生産効率を向上させることができます。